
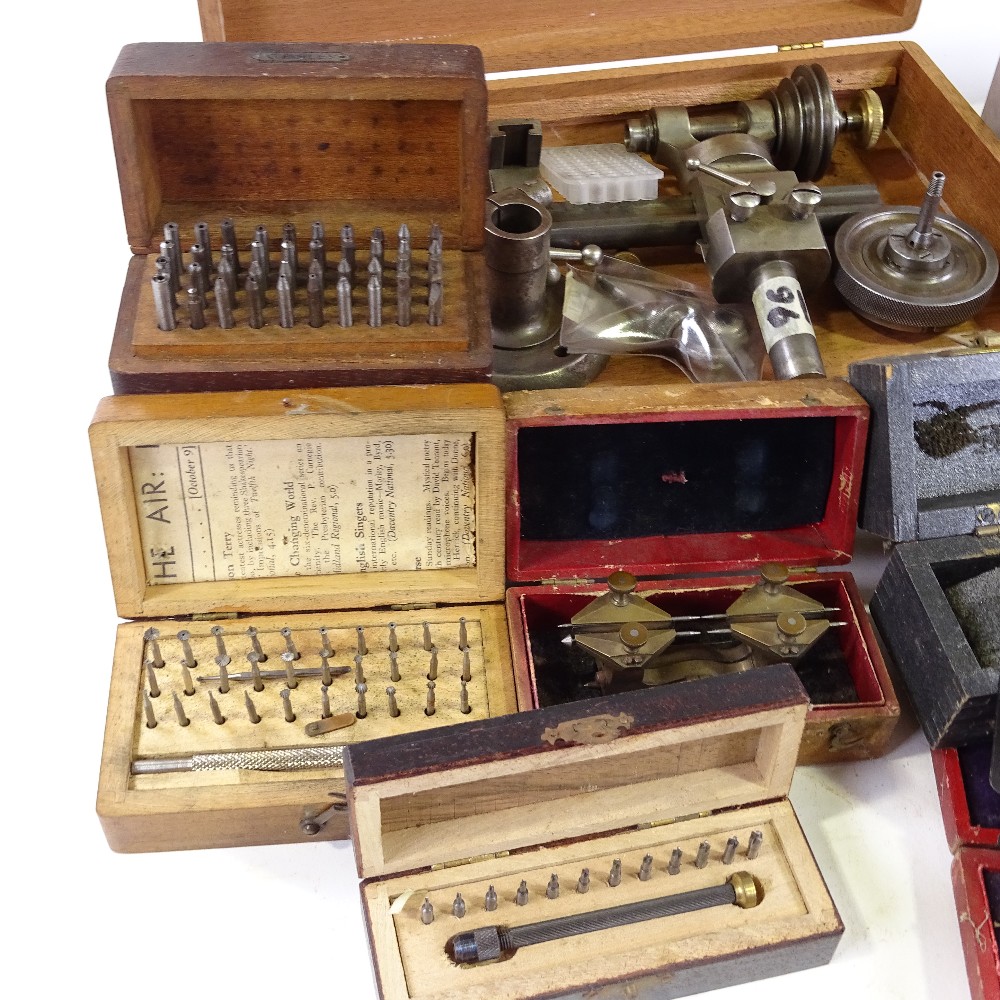
With so much certainty of measurement, is it even possible to adjust the cutting equipment with a similar degree of confidence? Using the turns, the watchmaker works with a hand-held cutter. Consider that when measuring at micron level, temperature change from as little as a ray of sunlight passing over a stone measuring table or the hand of an operator resting on a cast-iron instrument body translates into a dimensional change immediately manifest to the metrologist. Cocooned deep inside the premises, these areas are specially air-conditioned, with access only by air lock, to minimise variations in temperature. Today, I would argue that the most holy element of the entire operation in all serious manufacture is the metrology department. By taking production samples of parts at different times, the extreme sensitivity of an instrument like LeCoultre’s will reveal gradual dimensional changes that might suggest, for example, that cutters are getting blunt or that the machine’s “stops” (which limit the extent of cutter movement) have shifted. When producing parts in quantity, not only must the dimension of each one fall within a specified range, but all the tooling, the cutters, jigs and gauges, need to be tested and checked throughout to ensure consistency from batch to batch and, indeed, between the beginning and end of a production run. He was a pioneer of the nascent industrialisation of the craft. Remember that LeCoultre’s aim was not the repair of individual watches nor the fabrication of one-offs in the manner of Daniels.
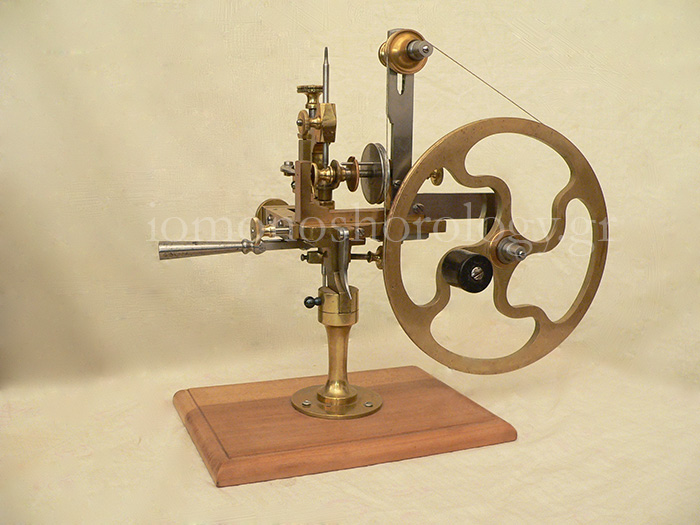
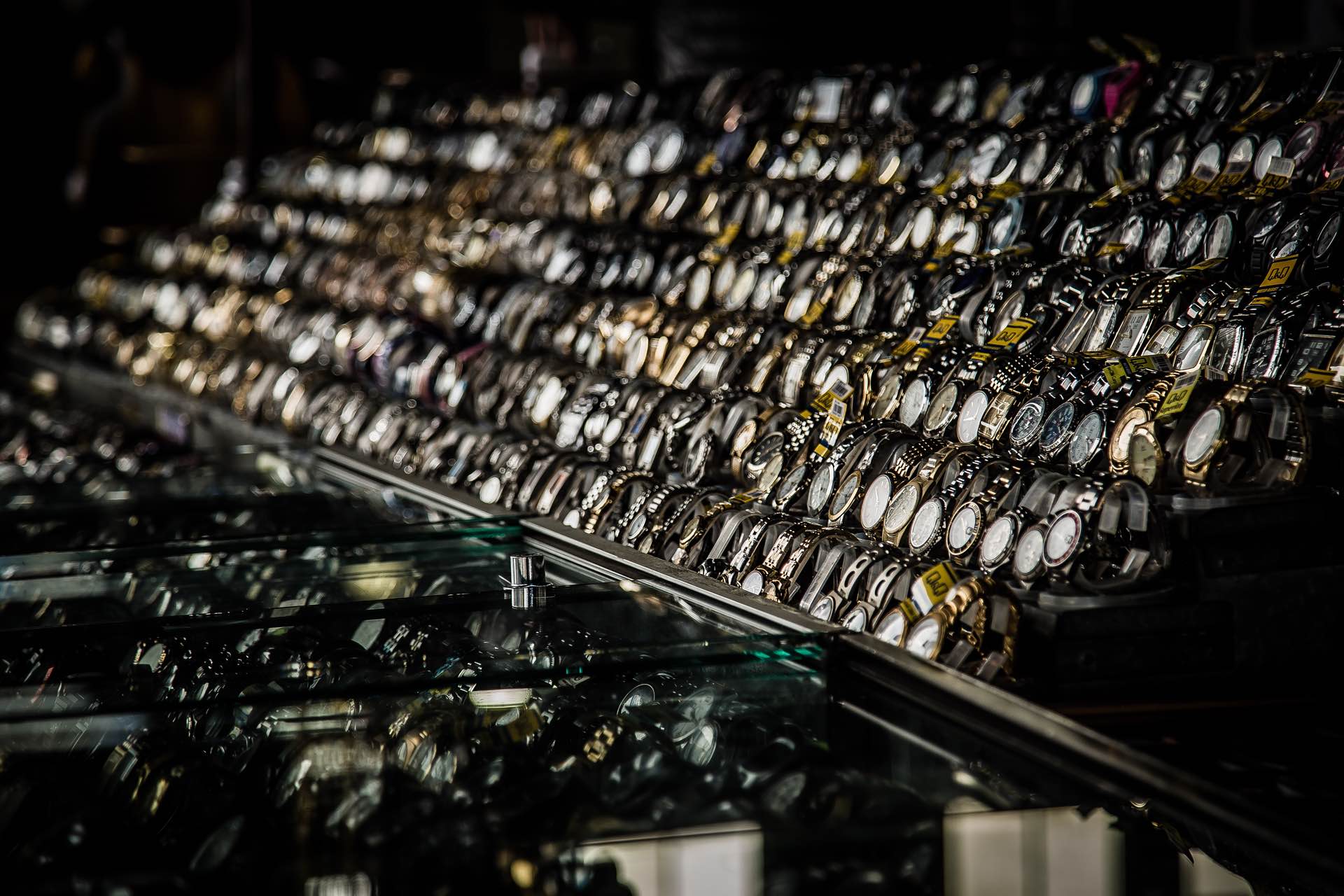
The Americans, and later the Swiss, began to develop tools and machines capable of producing vast numbers of respectable-quality watches. In the 19th century, the world’s top watches were being made by hand in the northern English towns of Prescot and Coventry, with London as their shop window. Patek Philippe, for example, use Computer Numerical Control (CNC) to make some arbors and pivots close to final size, and then bring them to perfect fit with their bearing jewels by hand-burnishing.Ĭrude so-called “cork and nail” methods, as romantic as they are, fall down the moment any attempt is made to scale-up production. This process is still carried out in an abbreviated way at the very top end of the industry. This rudimentary method was responsible for the production of navigational-grade instruments in the 19th and 20th centuries whose timekeeping performance was regularly in the range of tenths of a second per day, vastly better than all but the very best mechanical watches made today. This fettling and fine-tuning continues until all of the clearances and fits are absolutely flawless. The work of handcraftsmen like George Daniels is the product of one-off production, where each part is mated with its neighbour in a patient succession of “fitting”.

As crude as the three-nail method, or indeed the watchmaker’s turns, may seem, they are capable of producing parts of perfect circularity with zero deviation from the centreline, something impossible even with more sophisticated equipment. The solution: three nails hammered into the workbench and suitably bent made an acceptable substitute for the basic type of turning that was their stock work.
HOROLOGY TOOLS HOW TO
The next problem to overcome was how to do any work without his staple tool. With the family’s housekeeping budget thus shattered, a fellow in this predicament would be forced to pawn his most valuable tool, the turns (a type of lathe), in order to spare himself an injurious domestic lambasting. James Arnfield, one of the elder statesmen of English horology, tells of how pre-20th-century watchmakers in the north of England would regularly blow their weekly wages in the pub. One of watchmaking’s great ironies is that the most precise and beautiful watches can be, and often were, made using the crudest of tools.
